KTW Hochvakuum-Laserschweißgerät:
Präzision, höchste Schweißqualität und Kosteneffizienz in einem
Profitieren Sie von den Vorteilen zweier hochentwickelter Technologien in einem. Das Vakuum-Laserschweißen bietet eine präzise und kontrollierte, spannungsarme Möglichkeit zum Verbinden einer großen Anzahl verschiedener Materialien, einschließlich sauerstoffaffiner und hochschmelzender Metalle. Es eignet sich für eine Vielzahl von Anwendungen, sogar für Sensorik und andere empfindliche Komponenten. Und das zu einem erschwinglichen Preis.
Laser = Fortschritt mit Lichtgeschwindigkeit
Es gibt kaum eine Technologie, die in den vergangenen Jahren und Jahrzehnten so viel Fortschritt aufzuweisen hat, wie die Lasertechnologie.
- die verfügbare Leistung und Brillanz der Laserquellen und damit die möglichen Anwendungsfelder nehmen stetig zu
- die Anzahl verfügbarer Lasertypen und die damit einhergehenden Wellenlängen nehmen zu, wodurch mehr und mehr Werkstoffe bearbeitet werden können bzw. die Energieabsorption optimiert werden kann
- die Qualität und Ausprägung optischer Elemente nimmt stetig zu und damit die Fähigkeit den Laserstrahl zu modifizieren, zu manipulieren und u steuern
Die Energie des kohärenten Lichtstrahls hat bereits heute einen festen Platz in vielen industriellen Anwendungen (Schneiden, Schweißen, Strukturieren, und Beschriften). Doch Lasertechnologie ist eine der Zukunftstechnologien und die vielfältigen Forschungen und Entwicklungen werden den Strom der Innovationen über die nächsten Jahre nicht abreißen lassen.
Einen Beitrag zu diesem Fortschritt leistet auch die KTW Technology GmbH mit dem innovativen Laserstrahlschweißen von metallischen Werkstoffen im Vakuum. Es werden hier gezielt die Vorteile des Laserstrahlschweißens mit den Vorteilen des Vakuumschweißens kombiniert. Das Ergebnis ist ein neuartiges, flexibles Schweißverfahren, dass auch den höchsten Qualitätsanforderungen gerecht werden kann.
Die Zukunft des Schweißens, jetzt für Sie verfügbar
Der Hochvakuum-Laserstrahlschweißer von KTW Technology kombiniert die neueste Laserschweißtechnologie mit den Vorteilen des Vakuumschweißens.
Dank der großen Fortschritte, die in den letzten Jahren in der Lasertechnologie gemacht wurden, ist sie für die Anwendung beim Schweißen perfekt geeignet geworden. Das Laserschweißen verbindet die Fähigkeit zur zeitlich genau abgestimmten und gezielten Energieabgabe mit geringem Stromverbrauch und reduzierter mechanischer und elektromechanischer Beanspruchung des Zielmaterials. Als Methode zum Fügen von Metallen gut etabliert, haben Verbesserungen in Bezug auf Leistung, Brillanz, Qualität, Design und Kontrolle das Laserschweißen für weitere Anwendungsbereiche und Materialien erschlossen, darunter – in zunehmendem Maße – auch Kunststoffe.
Die Verwendung im Vakuum reduziert die ohnehin schon geringe Material- und Nahtreaktivität des Laserschweißens noch weiter. Das Ergebnis sind Schweißnähte mit einer unvergleichlichen Präzision, Reinheit, Homogenität und Haltbarkeit.
Wir bei KTW Technology sind bestrebt, unseren Kunden diese brillante Technologie mit der weltweit einzigen kosteneffizienten laserbasierten Schweißlösung unter Hochvakuum zur Verfügung zu stellen.
Kombination der Verfahren bringt Vorteile
Die Vorteile des Laserstrahlschweißen sind weitläufig bekannt und haben zu einer breiten Anwendung dieser Technologie beim Schweißen von Metallen und zunehmend auch Kunststoffen geführt. Der Laserstrahl überzeugt insbesondere durch den hohen Energieeintrag ohne mechanischen und elektro-mechanischen Stress für das Bauteil bei gleichzeitig geringem Energieverbrauch.
Schweißen unter Vakuum steigert die Güte der Schweißnaht durch die Vermeidung ungewollter Reaktionen der Schmelze mit der umgebenden Atmosphäre. Dabei korreliert die Qualität der Schweißnaht mit der „Qualität“ des Vakuums. Neben der Verarbeitungsqualität der Schweißkammer (geschlossener Raum) limitiert vor allem die Bereitstellung der thermischen Energie das erreichbare Vakuum-Niveau.

Verfahrensvorteile auf einen Blick:
Mit der Kombination der Laserstrahl- und der Vakuumschweißtechnologie werden nicht nur die Vorteile beider Verfahren verbunden, sondern es entstehen weitere signifikante Nutzenaspekte – getreu dem Motto: „Das Ganze ist mehr als die Summe der Einzelteile!“
Das Laserstrahlschweißen im Vakuum setzt neue Standards für das anspruchsvolle Schweißen von anspruchsvollen und sensiblen Materialien und Bauteilen.
Schweißen mit Laserstrahl | Schweißen im Vakuum |
---|---|
|
|
Kombination von Laserstrahl- und Vakuumschweißen | |
|
Vorteile der KTW Hochvakuum-Laserschweißtechnik
Die Stärke dieses Schweißverfahrens liegt in der Kombination von zwei verschiedenen Technologien. Das Laserstrahlschweißen und das Schweißen im Vakuum bieten jeweils für sich genommen Vorteile gegenüber dem Elektronenstrahlschweißen. Durch die Kombination der beiden Verfahren werden Synergieeffekte erzielt, die zu einem Ganzen führen, das mehr ist als die Summe seiner Teile.
Kontrolle und Präzision
Die Laserstrahlschweißgeräte von KTW ermöglichen eine präzise, wiederholbare, schnelle und einfache Positionierung des Laserstrahls auf dem Zielobjekt über CNC-Achsen. Darüber hinaus ist die Energieverteilung im Strahl ähnlich unkompliziert zu manipulieren. Das Ergebnis ist eine einfache und verlustfreie Übertragung der Schweißenergie von der Quelle zum Ziel. Kurzum, das Hochvakuum-Laserschweißen bietet einen hohen Grad an Automatisierung, Präzision und Wiederholgenauigkeit.
Darüber hinaus sind die Wellenlänge des Strahls und das Vakuumniveau je nach Materialbedarf, Absorptionsrate und Prozessanforderungen einstellbar, mit einem Maximum von 10-5 mbar. Das Schweißen im Vakuum macht auch die Verwendung von Schutzgas überflüssig, obwohl auch die Möglichkeit besteht, bestimmte Atmosphären einzustellen oder Schutzgase einzuführen.
Hohe Reinheit und Langlebigkeit
Das Schweißen im Vakuum fördert die Ausgasung des geschmolzenen Materials und verhindert ungeplante chemische Reaktionen zwischen der Schmelze und der sie umgebenden Atmosphäre. Außerdem werden Fremdeinschlüsse in der Schweißnaht verhindert, und die Neigung zur Porenbildung bei großen Schweißtiefen wird deutlich reduziert. Außerdem ist das Hochvakuum-Laserschweißen unempfindlich gegenüber magnetischen und elektromagnetischen Feldern. Das Ergebnis: ein homogenes Schweißbild mit einer Nahtfestigkeit, die dem Grundwerkstoff nahe kommt.
Materialerhaltung
Das Laserschweißen liefert eine hohe Energiedichte im Brennpunkt. Die Schweißung wird durch Absorption im Zielmaterial ausgelöst, wodurch keine mechanischen Spannungen oder Vibrationen entstehen. Außerdem bleibt bei dieser Methode die Wärmeeinflusszone sehr klein, insbesondere bei der Verwendung von Laserpulsen, und das Risiko von Spannungen, Spritzern und Rissen wird verringert. Weniger Spannungen reduzieren wiederum den Bedarf an Nachbearbeitung.
Effizienz und Wirtschaftlichkeit
Beim Vakuumlaserschweißen können bei gleicher oder reduzierter Laserleistung große Schweißtiefen (z. B. bis zu 50 mm bei Stahl) erreicht werden. Außerdem verbraucht es im Vergleich zum atmosphärischen Schweißen weniger Energie. Die skalierbare Pumpstation ermöglicht eine schnelle Evakuierung der Schweißkammer, was zu geringen Ausfallzeiten zwischen den Schweißungen führt. Darüber hinaus ermöglicht die Technologie aufgrund ihrer hohen Energiedichte hohe Vorschubgeschwindigkeiten und kurze Bearbeitungszeiten. Schließlich bieten der modulare Aufbau und die geringe Größe der Anlage ein hohes Maß an Flexibilität bei einem niedrigen Preis und geringeren Betriebskosten im Vergleich zu verfügbaren Alternativen.
Auswahl des Schweißverfahrens
Die Liste alternativer Verfahren für das Schweißen sensibler und hochbeanspruchter Materialien und Bauteilen ist kurz. Lediglich zwei Fügeverfahren
- das Elektronenstrahlschweißen und
- das Laserstrahlschweißen im Vakuum
stehen zur Auswahl. Die folgende Gegenüberstellung hilft bei der technischen Einordnung.
Elektronenstrahlschweißen | Laserstrahlschweißen im Hochvakuum | |
---|---|---|
Kurzbeschreibung |
|
|
Vorteile |
|
|
Nachteile |
|
|
Laserstrahlschweißen im Hoch-Vakuum
Verfolgen Sie im Video das Entstehen einer 3-dimensionalen Schweißnahtgeometrie
Anwendungsbereiche für KTW Hochvakuum-Laserschweißgeräte
Das Hochvakuum-Laserschweißen eignet sich für sauerstoffaffine oder hochschmelzende Metalle sowie für gemischte Materialverbindungen. Zu letzteren gehören Stahllegierungen, rostfreier Stahl, Aluminium, Zirkonium, Titan, Beryllium, Wolfram, Molybdän, Tantal, Niob und Mischverbindungen.
Anwendbar ist die Technologie unter anderem in der Luft- und Raumfahrt/Astronautik, im Bereich Energie und erneuerbare Energien sowie im Automobil-, Motoren- und Turbinenbau. Darüber hinaus eignet es sich für die Elektronik, die Sensorik sowie die Medizin- und Wehrtechnik. Aufgrund der fehlenden mechanischen Belastung eignet sich das Vakuum-Laserschweißen besonders für Sensoren, empfindliche Elektronik und vakuumierte Hohlkörper wie Sensorgehäuse.
Unser Service für alle Ihre Laserschweißer-Bedürfnisse
Wenn Sie die Vorteile der KTW Hochvakuum-Laserstrahlschweißgeräte nutzen möchten, bieten wir Ihnen folgende Produkte und Dienstleistungen an:
- Schweißsysteme für Labore und Produktion
- Hilfe bei der Prozessvalidierung
- Testschweißungen
- Auftragsschweißen in Kleinserie
- Hochfahren des Prozesses
Latest News
Patent EP 3723933 erteilt
Unter der Patentnummer EP 3723933 wurde uns das Europäische Patent „ Hochvakuumkammer, und Verfahren zum Betrieben einer Hochvakuumkammer für die thermische Bearbeitung eines Werkstücks mittels
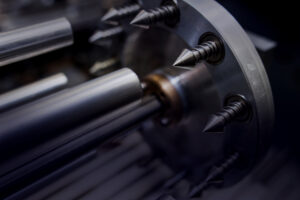
Welding: Vacuum vs. Atmosphere
The quality of a leaser welding seam depends on in which pressure environment it happens. See in the video the difference between welding in vacuum
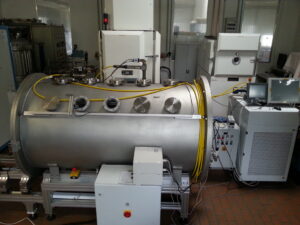
Innovation im Laserschweißen
Das Branchenportal: „Home of Welding„, hat einen Bericht über unsere Innovation im Laserschweißen veröffentlicht. Hier der Bericht im BranchenportalDer Bericht stellt heraus wie unser Schweiß-System
Sind Sie interessiert oder haben Sie Fragen?
Wenn Sie uns Ihren Namen und Ihre Telefonnummer hinterlassen, werden wir uns umgehend mit Ihnen in Verbindung setzen.