KTW High-Vacuum Laser Welder:
Precision, Highest Weld Quality, and Cost Effectiveness Combined
Enjoy the benefits of two sophisticated technologies in one. Vacuum laser welding offers a precise and controlled, low-stress way of joining a large number of different materials including oxygen-affine and refractory metals. Suitable for a wide range of applications, even sensorics and other sensitive components. With an affordable price tag to boot.
Laser = progress at the speed of light
There is hardly any technology that has made as much progress in recent years and decades as laser technology.
- the available power and brilliance of laser sources and thus the possible fields of application are constantly increasing
- the number of available laser types and the associated wavelengths are increasing, which means that more and more materials can be processed or the energy absorption can be optimised
- the quality and design of optical elements is constantly increasing and with it the ability to modify and manipulate/control the laser beam.
The energy of the coherent light beam already has a firm place in many industrial applications (cutting, welding, structuring, and marking). But laser technology is one of the technologies of the future and the diverse research and developments will not let the stream of innovations stop over the next few years.
KTW Technology GmbH is also making a contribution to this progress with the innovative laser beam welding of metallic materials in a vacuum. Here, the advantages of laser welding are combined with the advantages of vacuum welding. The result is a new, flexible welding process that can meet even the highest quality requirements.
The Future of Welding, Available to You Now
The KTW Technology High-Vacuum Laser Beam Welder combines the latest in laser-welding technology with the benefits of vacuum welding.
Thanks to great strides that have been made in laser technology in recent years, it has become perfectly suited for the application in welding. Laser welding combines the ability to use precisely timed and targeted energy output with low power consumption and reduced mechanical and electro-mechanical stress on the target material. Well established as a method for joining metals, improvements in power, brilliance, quality, design, and control have opened up laser welding to additional fields of application and materials, including - increasingly - plastics.
Using it in a vacuum reduces the already low material and seam reactivity of laser welding even further. It results in welding seams with an unparalleled precision, purity, homogeneity, and durability.
Here at KTW Technology, we strive to make this brilliant technology available to our clients with the world’s only cost-efficient laser-based welding solution under high vacuum.
Combination of processes has advantages
The advantages of laser beam welding are widely known and have led to a broad application of this technology for welding metals and increasingly also plastics. The laser beam is particularly convincing due to the high energy input without mechanical and electro-mechanical stress for the component and at the same time low energy consumption.
Welding under vacuum increases the quality of the weld seam by avoiding unwanted reactions of the melt with the surrounding atmosphere. The quality of the weld correlates with the "quality" of the vacuum. In addition to the processing quality of the welding chamber (closed space), it is above all the provision of thermal energy that limits the achievable vacuum level.

Process advantages at a glance:
The combination of laser beam and vacuum welding technology not only combines the advantages of both processes, but also creates further significant benefit aspects - true to the motto: "The whole is more than the sum of the individual parts!"
Laser beam welding in a vacuum sets new standards for the sophisticated welding of demanding and sensitive materials and components.
Welding with laser beam | Welding in vacuum |
---|---|
|
|
Combination of laser beam and vacuum welding | |
|
Benefits of the KTW High-Vacuum Laser Welder Technology
The strength of this welding method lies in the combination of two different technologies. Laser beam welding and welding in a vacuum each offer advantages over electron beam welding on their own. Combining the two creates synergistic benefits that result in a whole that is greater than the sum of its parts.
Control and Precision
KTW laser beam welders allow for precise, repeatable, fast, and easy positioning of the laser beam on the target via CNC axes. In addition, manipulation of the energy distribution across the beam is similarly uncomplicated. This results in easy and lossless delivery of welding energy from the source to the target. In short, high-vacuum laser welding offers a high level of automation, precision, and repetition accuracy. Furthermore, the beam wavelength and vacuum level are adjustable according to material needs, absorption rate, and process requirements, with a maximum of 10-5mbar. Welding in a vacuum also eliminates the need for shielding-gas use, though the possibility to set specific atmospheres or introduce inert gasses also exists.
Darüber hinaus sind die Wellenlänge des Strahls und das Vakuumniveau je nach Materialbedarf, Absorptionsrate und Prozessanforderungen einstellbar, mit einem Maximum von 10-5 mbar. Das Schweißen im Vakuum macht auch die Verwendung von Schutzgas überflüssig, obwohl auch die Möglichkeit besteht, bestimmte Atmosphären einzustellen oder Schutzgase einzuführen.
High Purity and Durability
Welding in a vacuum encourages the outgassing of the molten material and prevents unplanned chemical reactions of the melt and its surrounding atmosphere. It also inhibits foreign inclusions in the weld seam and the tendency to form pores at large welding depths is significantly reduced. Furthermore, high-vacuum laser welding is impervious to magnetic and electromagnetic fields. The result: a homogeneous welding pattern with a seam strength close to the base material.
Material Conservation
Laser welding delivers high energy density at the focal point. The weld is initiated via absorption in the target material, which produces no mechanical stress or vibrations. Additionally, this method keeps the heat-affected zone very small, especially when using laser pulses, and reduces the risk for tension, spatter, and cracking. Less stress, in turn, reduces the need for post-processing.
Efficiency and Economy
Vacuum laser welding is able to produce high welding depths (e.g. up to 50mm for steel) at the same or reduced laser power. It also consumes less energy compared to atmospheric welding. The scalable pump station allows for quick evacuation of the welding chamber, resulting in little downtime between welds. In addition, the technology enables high feed speeds and short processing times due to its high energy density. Finally, the modular design and small size of the facility offer a high level of flexibility at a low price tag and fewer operating costs compared to available alternatives.
Selection of the welding process
The list of alternative processes for welding sensitive and highly stressed materials and components is short. Only two joining processes
- electron beam welding and
- laser welding in a vacuum
are available. The following comparison helps with the technical classification.
Electron beam welding | Laser Beam Welding in High-Vacuum | |
---|---|---|
Brief description |
|
|
Advantages |
|
|
Disadvantages |
|
|
High-vacuum laser welding
Follow the creation of a 3-dimensional weld seam geometry in the video
Areas of Application for KTW High-Vacuum Laser Welders
High-vacuum laser welding is suitable for oxygen-affine or refractory metals as well as mixed material compounds. The latter includes steel alloys, stainless steel, aluminum, zirconium, titanium, beryllium, tungsten, molybdenum, tantalum, niobium, and mixed compounds.
Applicable industries for the technology include aerospace and space/astronautics, the energy and renewables sector, as well as automobile, motor, and turbine construction. Furthermore, it is suited for electronics, sensorics, along with medical and defense technology. Due to the lack of mechanical stress, vacuum laser welding is especially suitable for sensors, sensitive electronics, and vacuumed hollow bodies like sensor housings.
Our Service for All Your Laser Welder Needs
If you would like to take advantage of KTW High-Vacuum Laser Beam Welders, we offer the following products and services:
- Welding systems for laboratories and production
- Help in process validation
- Test welds
- Small-batch contract welding
- Process ramp up
Latest News
Patent EP 3723933 erteilt
Unter der Patentnummer EP 3723933 wurde uns das Europäische Patent „ Hochvakuumkammer, und Verfahren zum Betrieben einer Hochvakuumkammer für die thermische Bearbeitung eines Werkstücks mittels
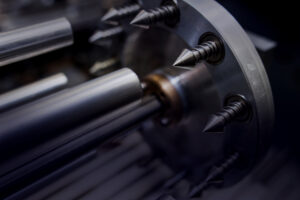
Welding: Vacuum vs. Atmosphere
The quality of a leaser welding seam depends on in which pressure environment it happens. See in the video the difference between welding in vacuum
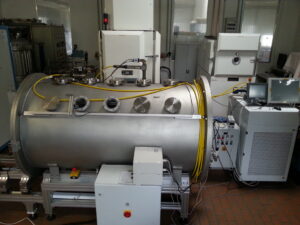
Innovation im Laserschweißen
Das Branchenportal: „Home of Welding„, hat einen Bericht über unsere Innovation im Laserschweißen veröffentlicht. Hier der Bericht im BranchenportalDer Bericht stellt heraus wie unser Schweiß-System
You have further questions and interested in high quality welding results?
Leave us your name and telephone number. We will get back to you as soon as possible.