The result of the 2nd generation high-speed dosing system from KTW Technology GmbH is an unrivaled, innovative dosing system with high application flexibility that meets today’s challenges in the beverage industry.
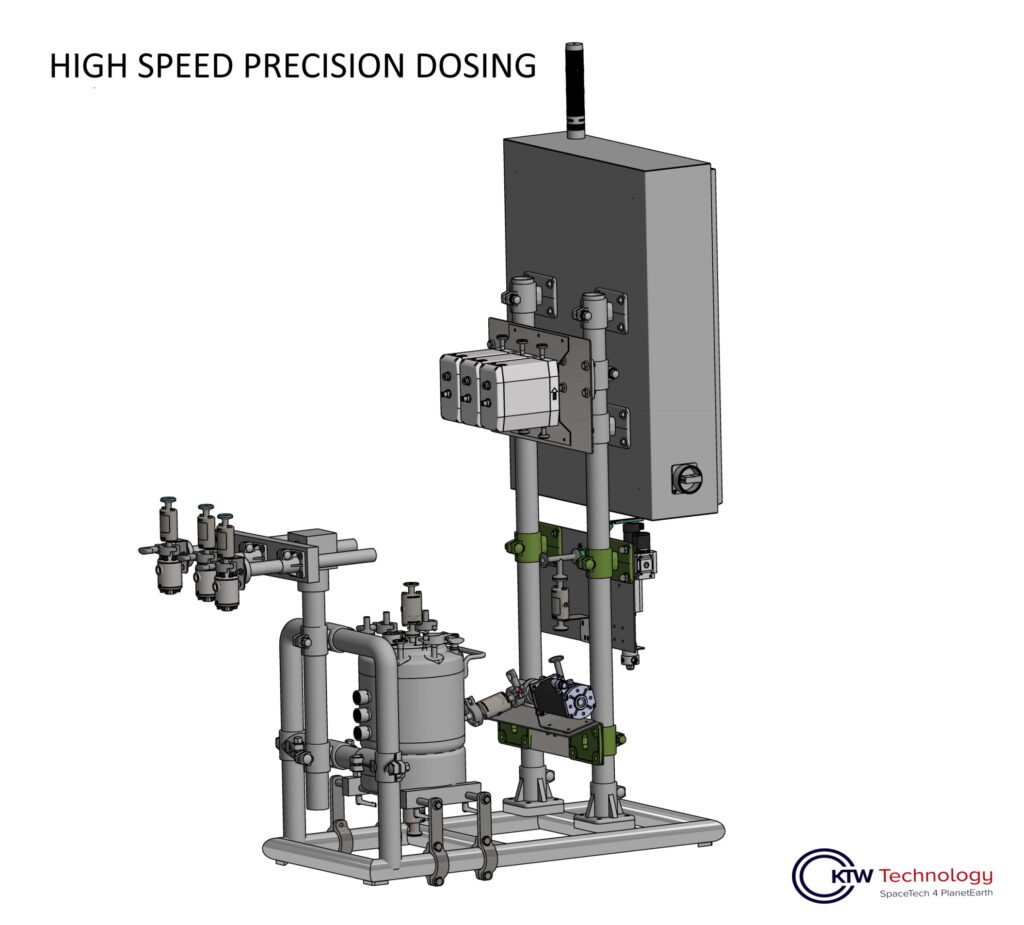
The plant has the following key features and is customizable.:
The dosing system consists of the supply unit and the valve station. The supply unit can be placed up to 20m away from the valve station. The valve station is mounted at the position where the valves dose the moving containers (bottles/cans).
Dosing into moving containers can be done both on a transfer starwheel of a filling line and on a linear conveyor (with minimal adaptation effort). Dosing can be done into empty as well as into already filled containers (e.g. additives, vitamins, flavors etc.).
The aggregate has the task of supplying the dosing valves with the dosing medium. In doing so, the pressure and the flow rates to the valves are controlled in such a way that an optimal dosing performance, according to the preset recipe, is achieved.
The valve station can consistigung of up to 3 dosing valves (expandable to 4 valves), whereby the relative position of the valves can be flexibly adapted to the specifics of the dosing point. Depending on the recipe, the valves can be used and combined in different sizes (dosing relevant).
For dosing at the transfer starwheel, the system has two sensors, a rotary encoder to determine the dosing position and adapt to the speed of the starwheel, and a container detection sensor. Adjustments to different configurations of transfer starwheels are made simply by entering the radius and number of positions on the starwheel in the program. After mounting the sensors, the system is ready for dispensing in a few minutes due to the simple configuration in the program.
For dosing on the linear belt, one sensor per valve and one encoder are required to adapt the dosing to the belt speed.
The dosing accuracy of the valves can range from +/-1% to +/-3%, depending on the valve size and the quantity dosed. To ensure this dosing accuracy relative to the dosing medium, the system has a calibration routine.
The shot accuracy/hit accuracy when dispensing at the transfer starwheel is +/-0.5 mm and can be guaranteed up to 1.4m/s container speed. Higher speeds can be achieved by adjusting the dispensed quantity to leave enough space to the edges of the container openings.
With the linear belt, the metering speeds are higher depending on the application.
The dosed quantities are measured by means of flow meters and written to a file, which can be evaluated to create measurement diagrams. The measurement accuracy is close to the valve accuracy.
The system reacts in real time to quantities that are not within accepted limits for various reasons, and sends a signal to the rejection system to remove non-compliant dosed containers.
To reduce waste of the dosing medium remaining in the unit, the system has a routine that allows dosing to the end (Aroma Quitting).
The cleaning of the system after the change of the dosing medium is carried out through the dedicated connection for the cleaning medium and is performed by an automatic routine that lasts a few minutes (parameterized times). Thus, the change of the dosing medium, with greatly reduced water consumption, is very fast.
To allow a high degree of flexibility, the plant can also be operated manually, so that each component of the system can be controlled separately.
The plant is equipped with a remote maintenance module, which allows remote access to the plant, enabling the import of updates, maintenance activities and troubleshooting.
The control is done with Siemens PLC and components, which guarantees a robust and durable operation. The availability of the components on the market is guaranteed for decades.