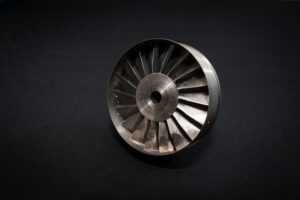
Story of TMC – Episode 5: Successful Implementation
In the history of the development of Titan Matrix Composites (TMC) there have been two successful implementations of this technology. The first implementation took place
The alternative to steel and other conventional materials for manufacturing industrial components. Smaller and lighter custom parts with increased longevity and great potential for fuel and energy savings. Also suitable for orthopedic implants.
Lightweight construction is finding its way into many technologies. The focus is particularly on thermally, mechanically and dynamically highly stressed components. Suitable lightweight materials make it possible to reduce the component geometry and/or the component weight, in each case without limiting the load-bearing capacity. The main materials to choose from are aluminium, carbon and titanium, which, however, differ significantly from each other in their material properties.
With the KTW TitanMatrixComposite , a new titanium-based material has now been added. The technical breakthrough of this type of material (Ti MMC), which has been worked on for decades in the aerospace industry, has so far been hindered by an unreliable and reproducible manufacturing process. KTW was able to overcome this hurdle with the development of the magnetron sputtering process.
In a world where energy usage is an increasingly important factor for the market success and profitability of products and technologies, materials that can replace steel and other heavyweight elements are sorely needed.
KTW Titan Matrix Composites are made up of SiC fibers inside a metal matrix, usually a titanium alloy. They combine the best of both worlds: the low specific weight of titanium with the fibers’ high tensile strength and stiffness. The result is a lightweight material with high homogeneity that retains its properties up to temperatures of 600°C and, due to its titanium surface, is corrosion resistant and biocompatible.
In addition, thanks to being manufactured using KTW Magnetron Sputtering, TMC components are able to adopt a variety of shapes. The results are parts that are just as strong or stronger than conventional alternatives while weighing a lot less, opening up huge potentials for energy and fuel savings for a wide range of industries and applications.
"Half as heavy and twice as strong as high-alloy steel -
and at temperatures up to 600° Celsius!"
Characteristics | TMC | High-strength Steel | Ti-alloy |
---|---|---|---|
Density in g/cm3 | 4 | 7,8 | 4,6 |
Strength in Mpa | 2200 | 1700 | 1100 |
Strength at 600°C in Mpa | 1400 | 800 | 650 |
Stiffness in Gpa | 210 | 190 | 115 |
Elongation in % | 1,3 | 6 | 15 |
Thermal expansation in K°-1 | 5 x 10-6 | 12 x 10-6 | 8,5 x 10-6 |
The material properties of the TMC require a specific component design.
Properties | Alu | TMC | Carbon |
---|---|---|---|
Weight | + | o | + |
Temperature resistance | - | ++ | - |
Strength | o | ++ | - |
Durability | - | ++ | o |
Stiffness | o | ++ | ++ |
Ductility | o | + | o |
Corrosion resistance | - | ++ | + |
Multi-dimensional load capacity | + | + | - |
Biocompatibility | - | ++ | - |
At the same dimensions, KTW Titan Matrix Composites possess 75% higher tensile strength and a 10% increase in stiffness than equivalent high-alloy steel components. This also means that, at consistent load, a significant reduction of component size is possible. In addition, TMC components show the same or better performance at high temperatures than their steel-alloy counterparts.
When compared with components made of high-alloy steel, TMC-built components on average weigh half as much at higher levels of rigidity. This allows fabricating large machinery such as plane turbines and other heavy duty appliances at a much lower weight, leading to great savings in energy and fuel in the final application.
The process is suitable for many kinds of components from all kinds of industries and processes. It delivers perfect and repeatable quality thanks to a high level of automation. Machining and 3D-printing allow the production of many desired shapes. Low reactivity and high biocompatibility also allow for usage in the medical field, for example, in artificial joints.
KTW Titan Matrix Composites are employable in a wide range of industries and fields:
In the history of the development of Titan Matrix Composites (TMC) there have been two successful implementations of this technology. The first implementation took place
We explained in the past episodes 1 to 3 what is TMC, the history of the delevopment and the technology behind it. In this episode
Over the past 30 years, titanium metal matrix composites (Ti MMCs) have been under considerable development and evaluation for use in aircraft engine and airframe
Leave us your name and telephone number. We will get back to you as soon as possible.